By Peter Walkden on 13 January 2022
Construction of service support frames requires the cutting of beam sections to prescribed lengths as per the intended design. SiFramo beam section is supplied Hot Dipped Galvanised in 6m lengths so when cut, leaves the cut end free of Zinc and exposed.
Generally, for special applications (e.g. outdoors, in coastal areas or aggressive atmosphere), section would be deemed to require some retrospective protection, usually a cold galv spray for HDG section. In siFramo's case, the section benefits from the technique of Cathodic Protection. Keep reading to find out the reason behind it!
Cathodic Protection: how does it work and what does it bring
Cathodic Protection works by means of an Electrochemical Cell where the base steel acts as the cathode and a sacrificial anode is employed. The sacrificial anode is generally separate from the metal surface with a connection through a cable or bolt.
In detail, the items to be protected from metal corrosion, are dipped in electrically conductive paint. A direct current field is applied between the material and a counter electrode. Finally, a closed paint film with excellent adhesive properties is created by the process.
What are the advantages?
- Outright and even coating even in cavities, at corners and edges
- Scratch, impact and hydrochloric acid resistant
- Clean-exhaust painting process
- CDP coated surfaces have ideal characteristics for follow on layers like powder coating
The benefit of cathodic protection for siFramo
Due to the thickness of the section being a maximum of 4mm, siFramo benefits from the Cathodic Protection technique.
On thicker sections, Cathodic Protection on a Hot Dipped section would not suffice as only the exposed steel close to the zinc coating would be protected (e.g. the edges of a cut traditional I-Beam would only see protection with patina forming on the central area).
As our section is a maximum of 4mm, the exposed cut end is always close to the surrounding zinc coating, so when there is an electrolyte present (in this case water) the zinc layer acts as the sacrificial anode, meaning the exposed cut ends is left free from attack.
Case study - installation on a costal environment
We have conducted a case study (at Lower Hutt, New Zealand), showcasing the Cathodic Protection process associated with our finishing first hand.
Through this test, a frame of siFramo was placed on a Lower Hutt Jetty to see the effects of the coastal environment on the product. The photo below shows a T-post arrangement with the ends of the section left untreated.
Six years after the installation onsite, it is clear that the cut ends do not show signs of corrosion, due to Cathodic Protection.
Lower Hutt Test Frame
It is worth noting that the brown discolouration is due to corrosion of the surrounding stand and pipe above, not of the Sikla section.
As a final note, if the raw end was to be painted for example, this would prevent the forming of the electrochemical cell. You would then end up seeing potential for more corrosion as zinc would not act as the sacrificial anode and you would be left with a very thin painted coating as protection.
HCP Protection Systems - Contact us for experienced support!
At Sikla we refer to “High Corrosion Protection” (HCP) to offer you the most effective corrosion protection.
To select the optimal surface coating for your demands, we attach great importance to the protective effect, the preservation of the functionality (e.g. mobility of the thread), market requirement and economic feasibility. Additionally, our preference is on state-of-the-art technologies that are environmentally friendly and that guarantee the most efficient and comfortable installation performance.
Should you need further guidance on the Cathodic Protection or other of the available coating options for metal corrosion protection, our team will find with you the most suitable solution.
Contact us for more information!
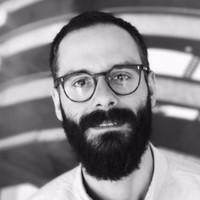
Comments