By Harry Starke on 22 September 2020
To conclude our blog series on siFramo, Sikla's modular steel system, Harry Starke will explain the benefits of choosing a branded product system within the construction industry.
Would you board a flight on an unbranded plane resembling a Boeing?
Imagine. A budget airline is offering a long-haul business class ticket to Los Angeles for $200. The catch is that the aircraft is a Dreamliner lookalike with no European or American approval, made somewhere in a Far East country called Absurdistan. Expressing your doubts, the airline produces copies of bad quality generic technical data to give you assurances that the ‘flight has worked many times before’.
Would you go for it? If you would, how relaxed would you be during the 8 or 10 hours on board?
What sounds like a joke is unfortunately the reality in many construction industry projects when it comes to safety relevant product systems like steel frames and brackets. For the past two decades, it has become a normality for certain companies to copy the design of light weight brackets and strut channel systems from established manufacturers to offer cheaper deals on installation consumables. End-users tend to focus on generic geometry and comparable prices such as ‘per metre’, ‘per length’ or ‘per 100 pc’ rather than questioning the raw material used, available certificates, technical data, let alone comparing prices for solutions on a full cost basis. The ‘Dreamliner’ above, calculated without R&D costs, no approval subscriptions and quality surveillance but, merely assembled based on copied plans and components, would indeed cut end-user prices dramatically. The same applies everywhere in manufacturing.
Would you buy a kit of smelly plastics, looking a bit like Lego, for your 8 year old?
No? But why, on the other hand, would you buy generic steel products from dubious sources for your client’s project?
Low disaster potential for as long as the typical application is light duty
This mentality has been working for such a long time because of relatively low risks in typical application areas of brackets and lightweight steel on one hand and high safety margins used by branded product manufactures on the other hand. For example, generic ‘Unistrut’ and rubber-lined pipe clips are typically used for small dimensioned building services of all kinds, with relatively low disaster potential.
Branded manufacturers typically use safety factors somewhere between 2 and 5 meaning that a published pay load of 1 kN (the equivalent of 100 kg weight force) could be based on an ultimate load of at worst 2 kN and at best 5 kN. Copying such a product’s design and making it from lower grade mild steel, perhaps using a slightly thinner steel coil, makes it therefore still unlikely that the supplier will face a complaint due to technical failure. Finally, the 1 kN component will most likely be used for a 0.2 kN application because the industry traditionally over-specifies, which is more down to idleness than to a desire for added safety.
Applying the same philosophy to heavy duty is shifting business risk from ‘financial’ to ‘operational’
Now I must make a confession: Sikla, have been feeding the beast. With the benefit of hindsight, it is questionable whether it was good idea to encourage those in the business of lightweight bracketry consumables to extend their product portfolio to cover heavy-duty applications too. It has worked well in some instances, where we find increased technical competence of the distributor in question, making them more solution orientated. Others however, and this applies to product manufacturers and their distributors alike, have not adapted their philosophy to the higher responsibility connected with heavy duty applications. Even worse, some have done the polar opposite, adapting the characteristics of the modular steel system on offer to their existing philosophy which is based on fixings, fastenings and light weight brackets.
What this does is, put simply, shifting the business risk from ‘financial’, i.e. the risk of losing profit margins or tenders due to higher buying prices, toward ‘operational’, i.e. the hazard risk associated with a heavy-duty steel support solution that is potentially not fit for purpose.
10 years ago, when the market for modular steel systems was still young, there was the choice between properly calculated old-fashioned steel, made by approved workshops, on one hand and less than a handful of well- known system suppliers, with healthy R&D budgets on the other hand. This included us, as well as a premium manufacturer located in the alps and one of the world leaders for ‘steel-to-concrete’ solutions.
Even today the above are the only product systems that have been accepted by heavy industries’ structural engineering departments who do not leave it to chance, or to an installation contractor's judgement what can be considered 'safe' or appropriate.
However, there is also the building services part of the construction industry and this is where fruit is traditionally hanging very low for protagonists of plagiarism and beneficiaries from generic lookalike products. Here, in what is by comparison a low regulation area, we find installation contractors in charge of skids for heavy pumps, brackets for large bore steam pipes or even off-site manufactured plant exposed to dynamic forces. Many of these companies’ site teams in charge are happy to sign off solutions proposed by suppliers who don’t know much about the mechanical properties of their product, the plausibility of it’s connection design let alone the grade and quality of raw materials used.
They don’t understand that load bearing steel can only be made thinner when corrugation and grade compensate for it, that frames are always just as strong as their weakest link or that connection positions are more relevant for rigidity than section size and must therefore be logical and easily checkable.
As a result, generic products are mushrooming. We find frames supporting heavy duty gear that merely meet visual engineering requirements when looking at them from a distance. Steel sections that deform just by the application of their own screws, elongated holes that are dimensioned and positioned in disregard of their structural impact, connecting elements that can too easily be combined with any fastener rather than a dedicated one.
Half-baked modular steel: weakest link= 1 bolt, section deforming by its own connection, inserted component not matching
For manufacturers and distributors who promote this approach, selling modular steel or heavy duty applications as if it were threaded bar or standard Unistrut, it is not a question if this will end in tears but when. This however assumes that they care, which cannot be taken for granted.
A Branded Product is not About Luxury but Accountability
For the best part of 10 years, Sikla have been focusing on a particular type of power plant where secondary steel design is challenging, pipe temperatures are high and so are cable weights. The first projects we supplied have undergone conversions and extensions. Plant operators find the name Sikla on all our components and, wherever they are in the world, they find us or at least an authorized representative.
Design from our product system can be verified as-built, compatibility remains guaranteed and so does the product quality itself whether it is the weld or the coating.
Using a branded product means access to third party test data, software plugins that consider all components and their properties, liability and a strong likelihood that the supplier will still be available even when the buyer of its product is not anymore.
Branded modular steel: Traceable, accurate, structurally calculable and no tampering potential.
It is no luxury to buy a branded modular steel system but statement of quality, traceability and accountability.
Be updated with our solutions and best practices recommendations. Visit and follow our LinkedIn pages today:
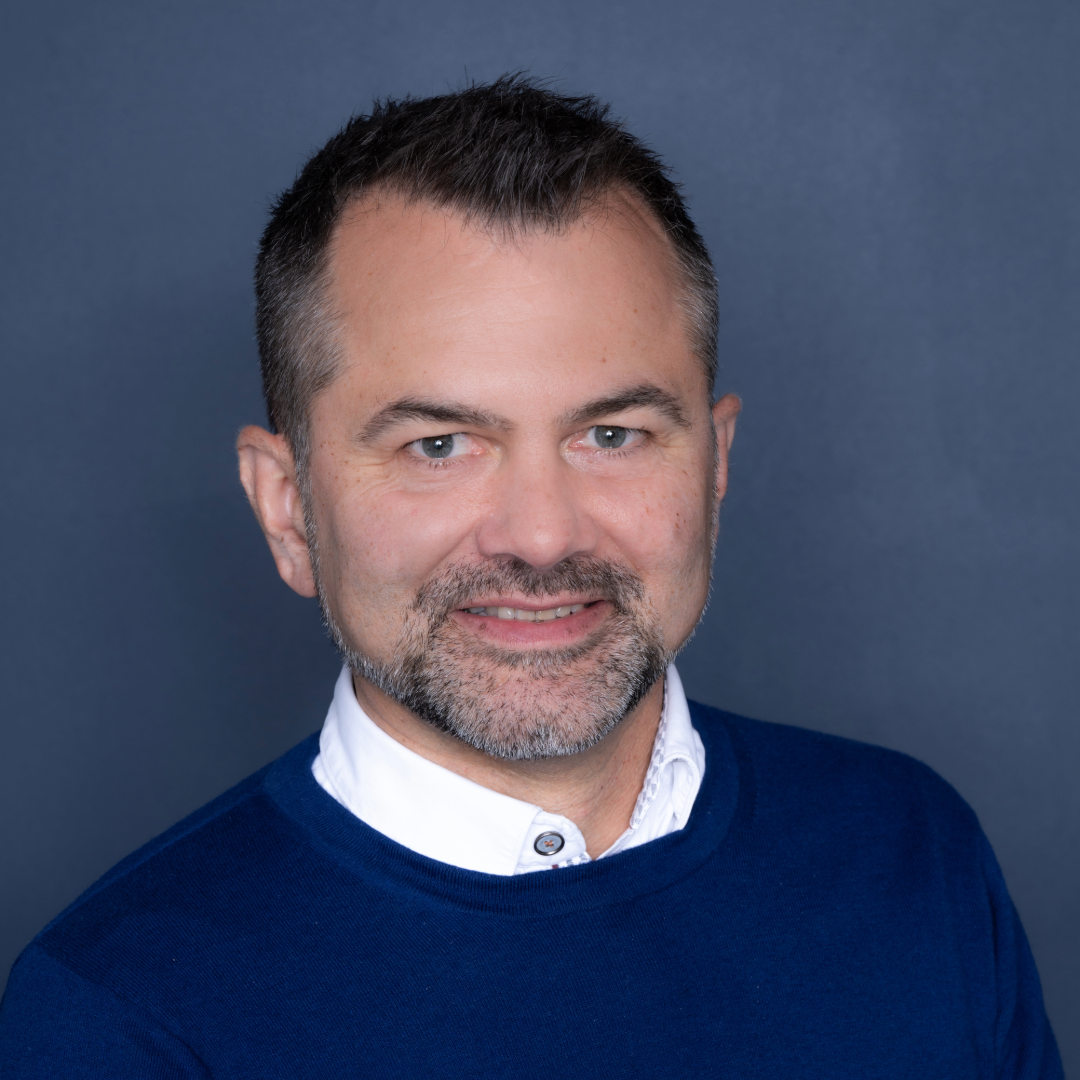
Comments