By Harry Starke on 23 November 2020
When it comes to above ground pipework, power stations have a unique combination of density and individuality. What does this mean?
Density means there are a lot of pipes per m3 compared to other buildings. As a result, a project with a small footprint that may be a small job for a roofing company, is nevertheless a large-scale piping design and installation challenge.
Individuality means, in this context, that there is a variety of pipe dimensions, temperatures, materials and combinations that one would struggle to find anywhere else in construction. If your concept of industrial pipework is a bank of several pipes, sitting in regular intervals on a steel structure, forget this in a power station. You will not find such level of repetition and simplicity here.
Mechanical Services in Power Stations Requiring Pipe Supports
These are the main services you can find in a Power Station that require the design and installation of Pipe Supports:
Pipework requiring support structures in power stations: large, small, hot, cold, left, right, up, and down – and mostly single.
Piping professionals in the Power Engineering industry distinguish between:- Primary pipe supports
Components required to ‘grab’ the pipe. In piping design these components are often referred to as ‘pipe attachments’ and they can be as simple elements as U-Bolts but also as complex ones as a so-called Constant Hanger. In most instances they are Pipe Shoes, i.e. a steel plate, -web and one or two clamps welded to it. - Secondary pipe supports
Components required to bridge the gap between the above 'attachments' and the building structure, i.e. the next available structural beam, concrete wall or floor. These supports are usually steel frames.
The first subject, apart from some potential to improve details, can be considered sorted. There is a global manufacturing industry offering engineered hangers and supports, including ourselves at SIKLA, with standardised and approved products that are not only available as the actual product but also as CAD blocks integrated into libraries or even plug-ins.
The other one however, secondary pipe supports, is a bit trickier. Designing a primary pipe support is relatively easy in so far as it can always be assumed that the secondary pipe support will be nearby. The secondary pipe support designer cannot assume anything: if the pipe must be installed in the middle of nowhere, the next ceiling, wall floor or structural beam being metres away, then it is what it is – there is only so much that can be standardised in this field.
For this reason, ‘secondary pipe supports’ have for long remained an outcast in a world where everything else turned into standardised products, supplied by globally available mass producers. Secondary pipe supports have been a text book example of what the saying ‘re-inventing the wheel’ means: time after time piping designers invented something new, just to integrate a pipe of a specific temperature and dimension into a building of a specific architecture.
This was until siFramo became available!
Leaving power engineering projects aside for a moment, the siFramo products’ efficiency increases with two factors:
- The variety of steel frame designs (100 frames out of 100 that are all of the same dimension would be the lowest variety whereas zero frames out of 100 having the same dimension of another frame would be the highest variety)
- The number of junctions/branches per meter of steel section (an inverted goalpost frame with 2 endplates that is 4 metres wide has a far lower number of junctions per metre compared to an F-shaped pipe stand that is just 1 meter high)
The above means that the closer you get to 100% variety of steel frames that are simultaneously short and have many branches, the more economically wise it is to opt in favour of siFramo. Likewise, and in all honesty, the closer a pipe support requirement is to 100% geometric uniformity whilst simultaneously having hardly any branches per metre steel section, the more likely it is that good old fashioned welded steel is the best option.
Now, coming back to this blogs’ subject: secondary pipe supports in power engineering projects. This is as close as one can get to the former, making siFramo the obvious first choice.
There are another 3 good reasons why siFramo should be your 1st choice for secondary pipe supports:
1. The characteristics and the simplicity of the product’s design that guarantees a uniform and reliable quality when using yet unknown sub-contractors to install, or even fabricate, the supports
2. The availability of plant software plugins that not only allows detailed piping design based on the details of the siFramo product, but even improves the design process’ efficiency by making it easier than designing conventional steel supports
3. The service package that the product is imbedded into, which allows the supports to be ordered exactly as fully fabricated as traditionally expected and as transparently calculated against a rate per kg, making this product in the first project a ‘known unknown’ rather than an ‘unknown unknown’.
Above: whoever makes a frame from siFramo, the quality will be reliably good – software plugins allow for detailed planning
The main power station components ‘Boiler’ and ‘Turbine’ have traditionally always required the detailed design of pipe supports. The same applies to the ‘Water Steam Cycle’ (WSC). High temperatures and 24 hours system operation in the future are too high a responsibility to be relaxed about this detail and to squeeze it into a future sub-contract’s small print. Therefore, these are the areas on the mechanical side of power engineering where all benefits from our siFramo system apply:
- More convenient support modelling and drafting in PDMS/E3D, SP3D or other plant software
- Cost reliability by being able to design against support-weight targets rather than having to know the pricing details of individual products
- Flexibility to decide in situ where, when and how to fabricate - without compromising the end product's quality
On top of this there are the general benefits of the system itself, such as significant weight reduction, ease, and speed of dealing with modifications, instant availability with full corrosion protection.
Traditional on-site chaos of pipe supports that cannot be modified versus orderly packaged siFramo with maximum flexibility
Finally, there is the Balance of Plant (BoP), whose mechanical side comprises instrument and service air systems, hydraulics, and heating and cooling systems. From the engineer’s perspective this would be called ‘General Piping’. Even a power stations is, after all, just a building.
The biggest difference to the main components referred to above are, in terms of the usage of siFramo, that General Piping’s support design is not considered as safety and system relevant, therefore often an ‘on-site design element’ to be resolved by sub-contractors under time pressure. We have observed a trend in recent years, that bigger clients migrate this subject into the detailed design phase but, in reality most BoP pipe supports in the world are being built tomorrow based on what was concluded to be the demand today.
A siFramo on-site consignment improves the quality of general piping supports designed and built by contractors in situ (right)
Should siFramo be used for mechanical services in your next power engineering project?
Given the number of such projects the system has already been used in, this is the wrong question. The right question is: where should we start using it?
At Sikla we understand secondary pipe support design is entrenched in the tradition of a complex planning process that varies from client to client. However obvious the benefits might be, switching after nearly a century of welded flanged steel design to a perforated Meccano style system is not a quick and not an easy decision for any client and for any project management team. However, the variety of main and auxiliary components within one power plant project bears the opportunity to try and learn. Perhaps the system has already been used in your last project and you are just not aware of it?
My recommendation:
Approach it like changing your fleet from fossil fuel to electrical vehicles: step-by-step. However small the first step, it is better than ignoring a trend that has become stronger and more widespread over the last ten years.
If you are interested in learning more about the system contact our team for further details. Maybe you can then consider including siFramo in the project you are currently working on!
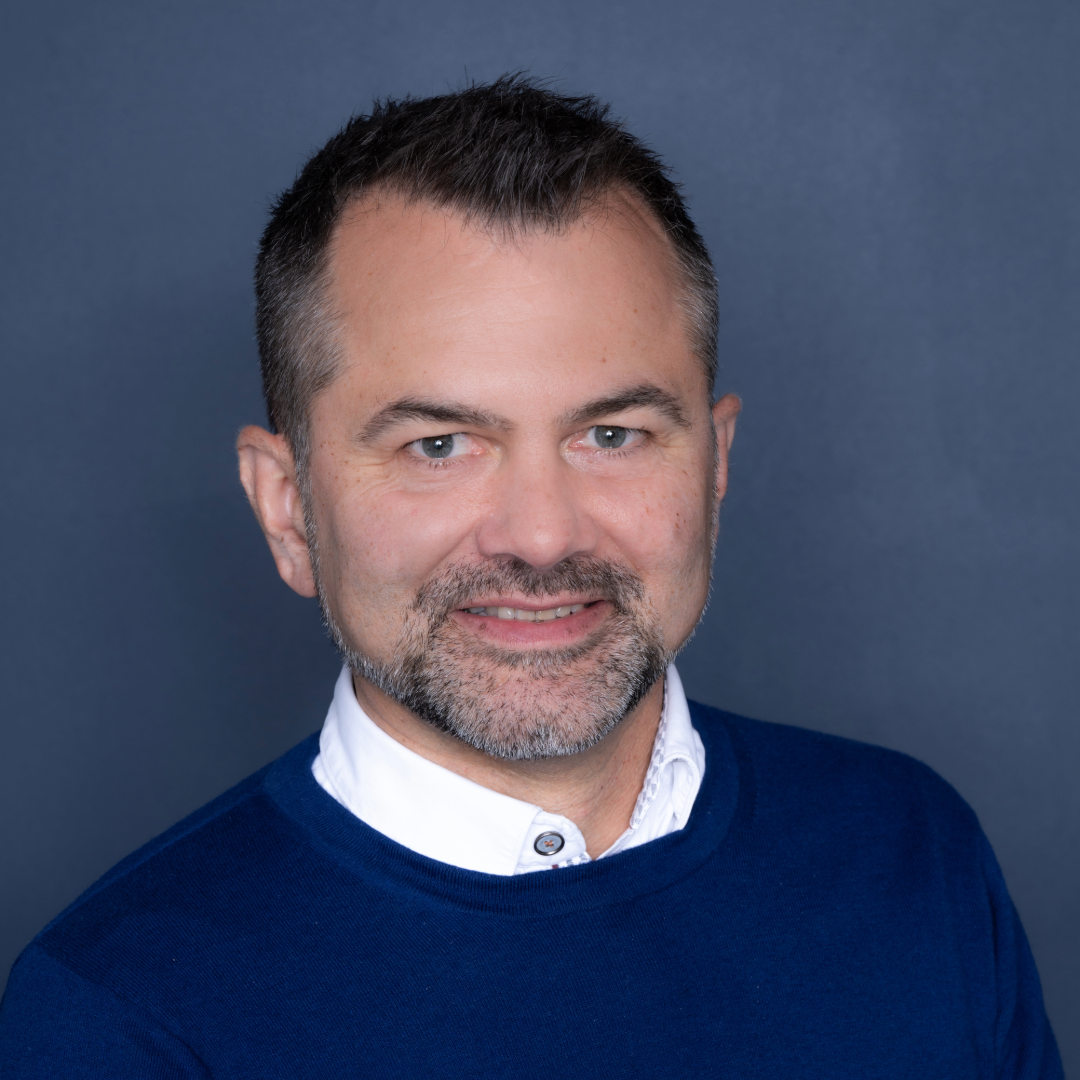
Comments